DFB
Well-known member
- Aug 12, 2019
- 5,083
- 3,367
- Thread starter
- #2,461
You know when it's a now or never situation and things end up at a point of no return............................
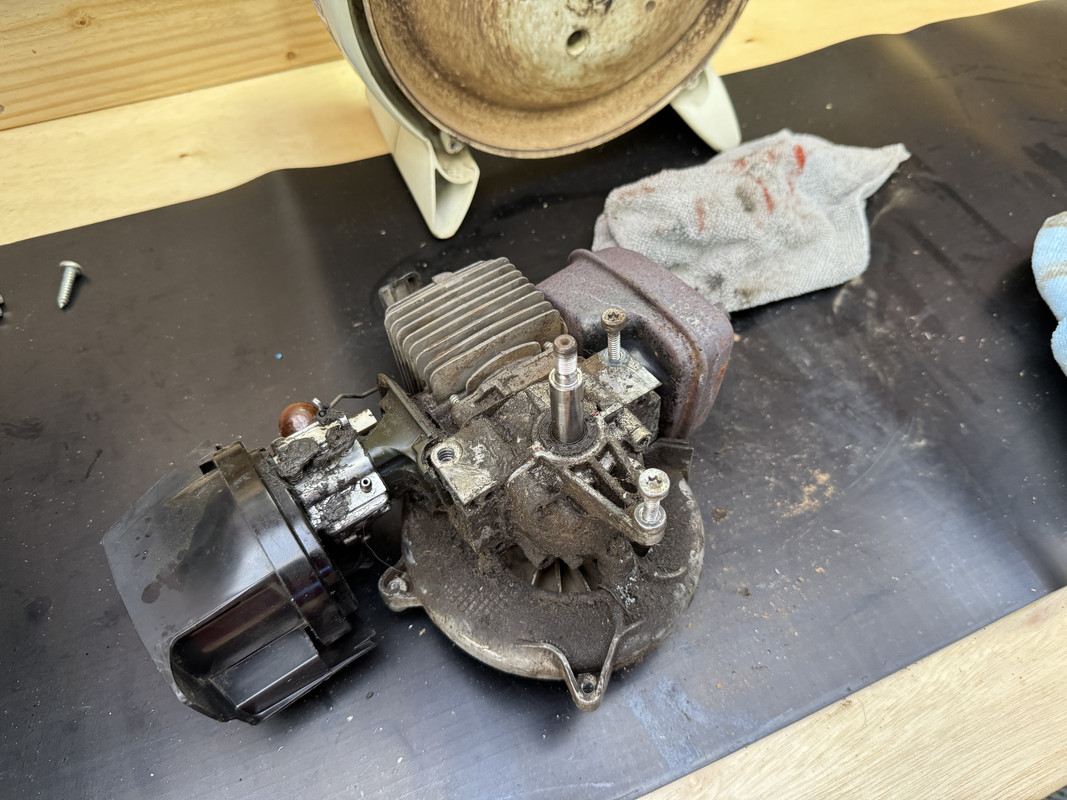
That is a complete engine assembly for a Stihl BG 86 blower sitting out of the plastic chassis. This machine I had to sideline for a brand-new blower because it kept breaking the recoil spring. I assumed it was something to do with the crankshaft bearings as something didn't feel right when pulling on the rope. I didn't have the time to mess about, so it got put away for parts.
A few weeks ago, I pulled it down and found that the engine was loose in the chassis, which was causing it to flex and twist when being pulled over, in turn putting more strain on the starter and starter spring. Hence the breakages. As I stripped it further, I then discovered someone (the dealer) had tried to remedy this with a coarse thread timber screw. Of course I was never told this. So, I thought perhaps I could have a go at doing this repair PROPERLY. Once again, this is why I am doing these jobs myself, no one gives a sh.t and I'm fed up paying for such incompetence.
This shows the damage caused, the timber screw had wallowed out the threads. There are three of these to hold the engine assembly to the blower frame, the hole should be for a M5 fastener, well its beyond M7 here...........
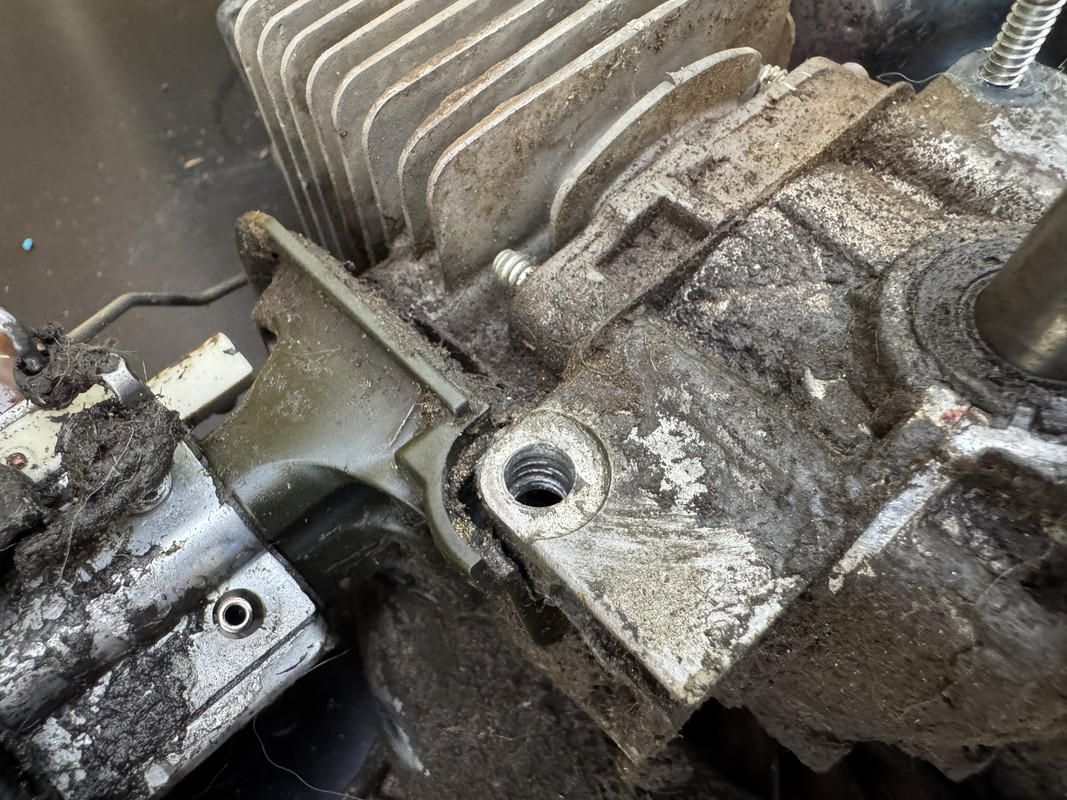
So, after some recommendations, I grabbed this Helicoil kit from Supercheap. Because of the damage, I had to go up to an M6 fastener, which I had on hand after buying an assortment of Stihl hardware last month.
(I paid cash for this kit, much to the bemusement of the young lad on the register, took him a while to figure out how much change to give me.
)
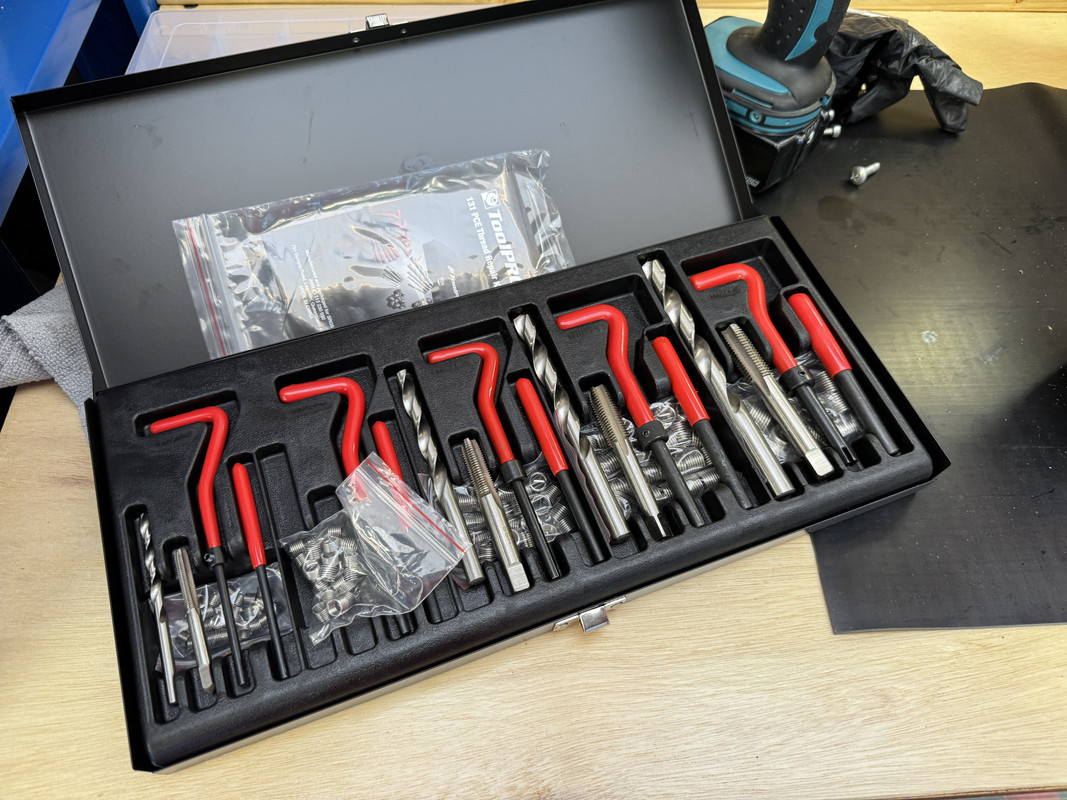
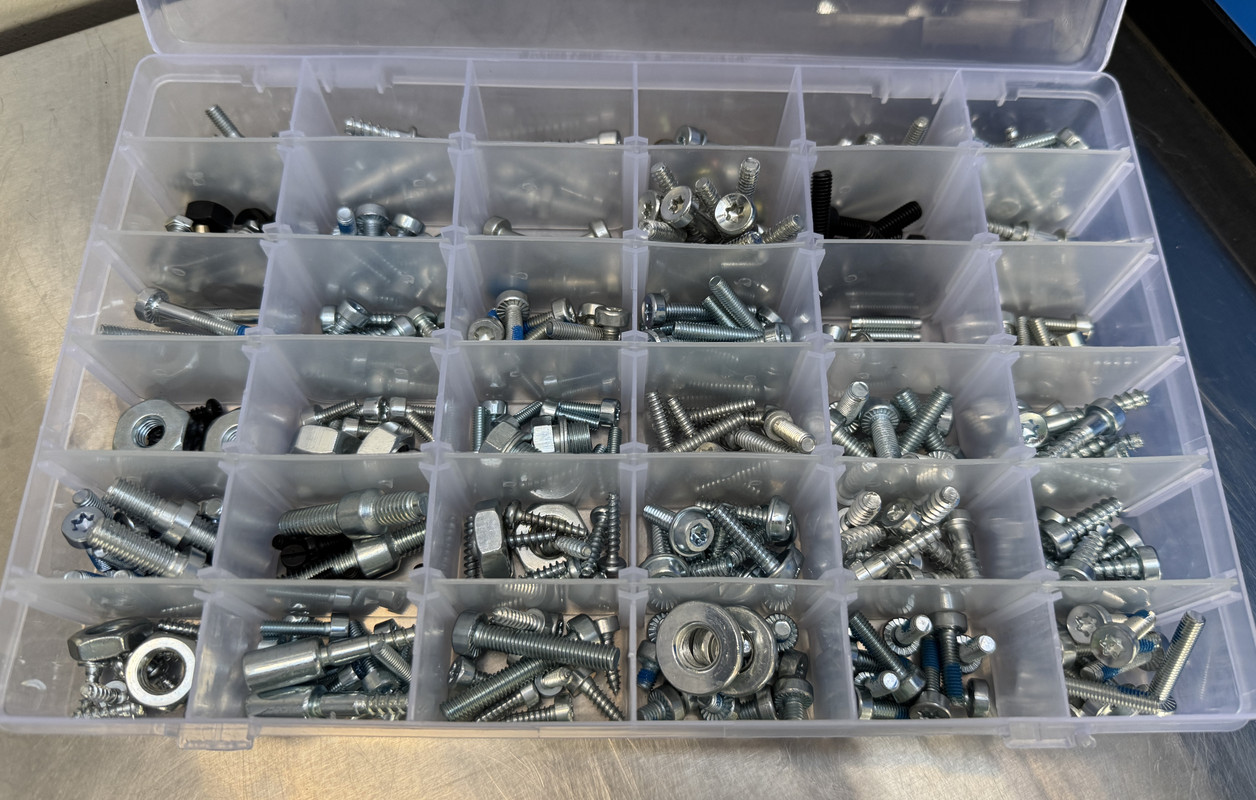
I have never used a Helicoil before, let alone a thread tap. Because of how flogged out the hole was, the supplied drill bit was only used to finish off the work of the wrongly used fastener. The tap threaded in and started cutting smoothly, which was used with some lubricant and the occasional back and forward to help it along. As always, I watched how to do this multiple times, many thanks to the Mr. Dactyl.....................
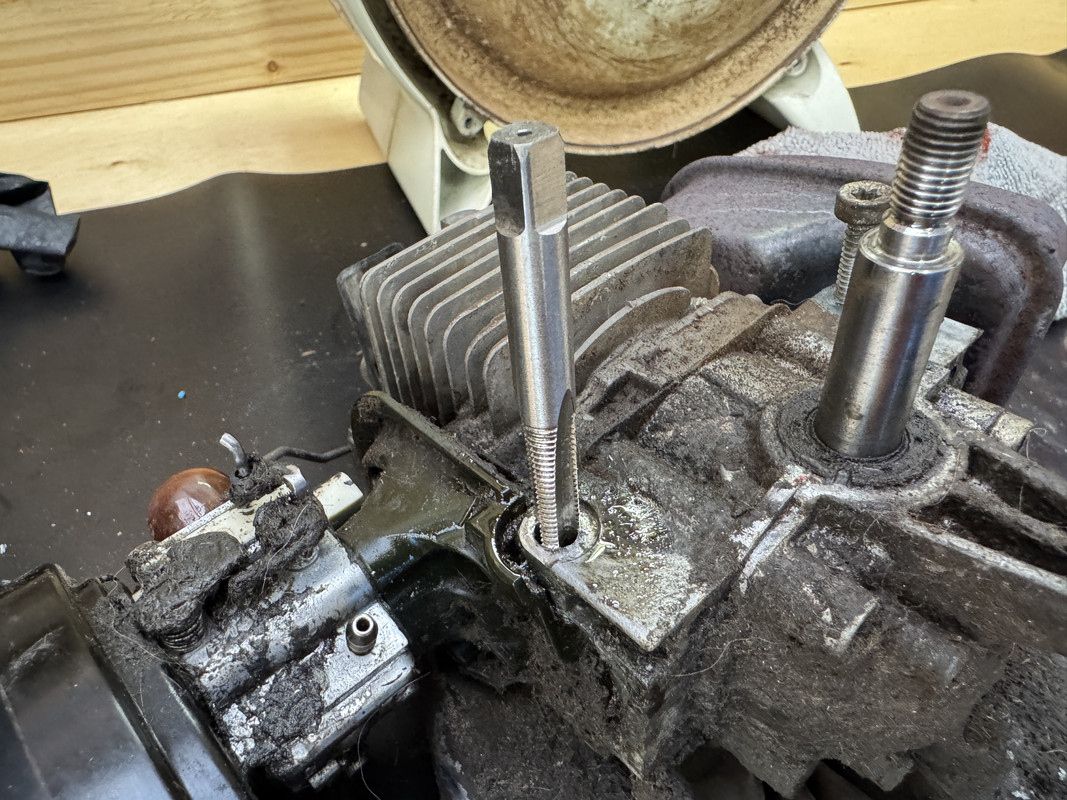
This hole is an external pass through, so no chance of metal chips entering the engine. The Helicoil insert is then wound in with the supplied install tool, the winding tab then broken free with the supplied punch. I had threads again!
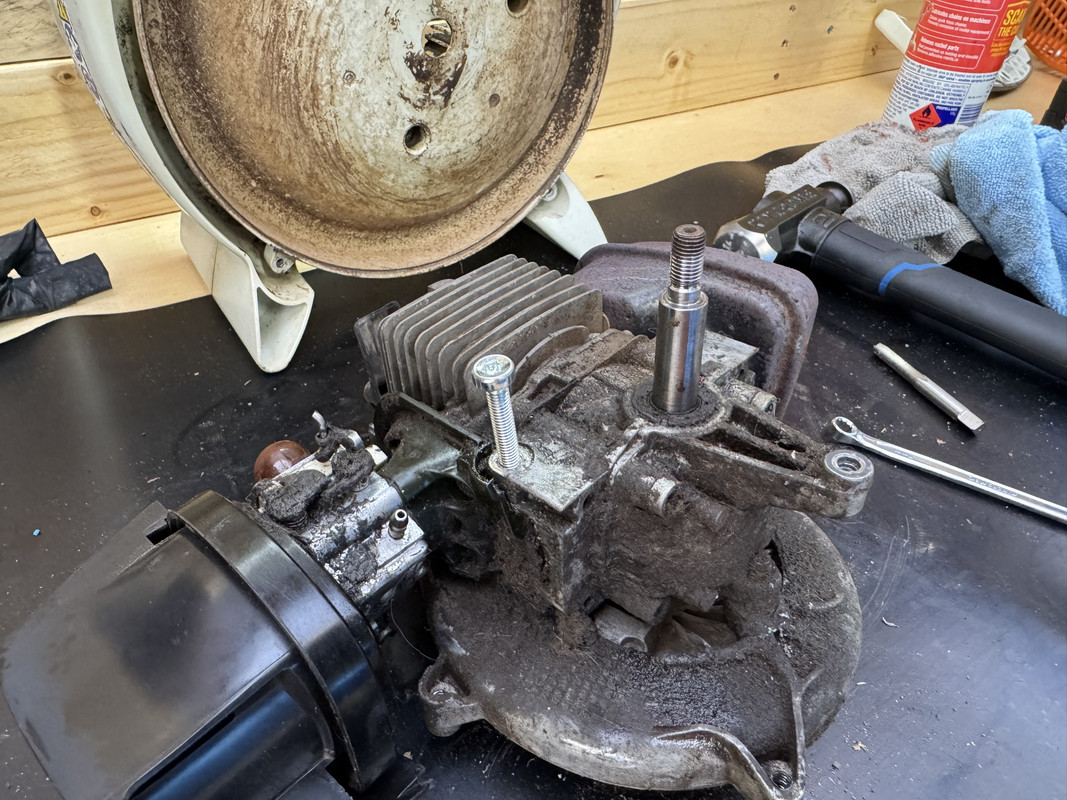
Then it was a case of putting it all back together again. This involves reconnecting the fuel lines before aligning the engine unit back into the frame and the bolts tightened down, the repaired threads torquing nicely. The fan is then put back on the crankshaft with a washer either side, followed by the reverse thread nut, followed by the fan cover. On the other side, the throttle rod is connected to the trigger and the kill wires hooked back onto the coil. From here, the front cover/recoil is reattached, and the blower tube reconnected, which on this machine needs the assistance of three tek screws to hold it in place.............the result of working a hard life.
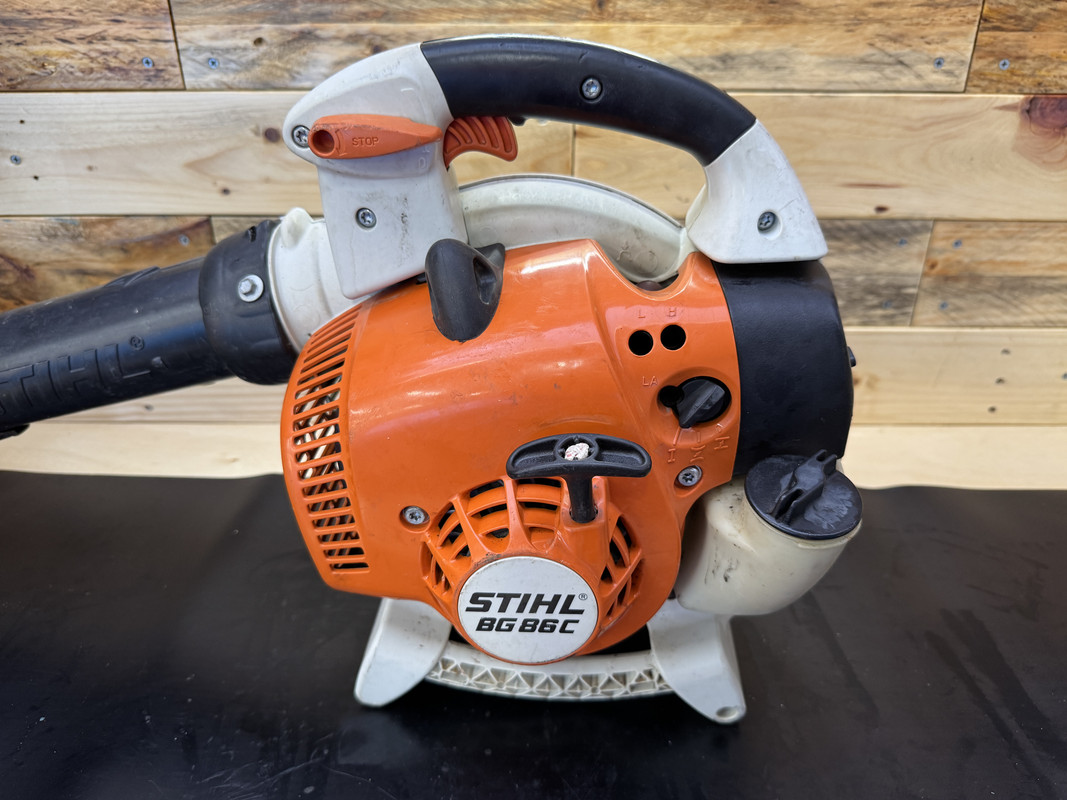
Having used and worked on countless examples of these blowers since 2002, I know them inside out. There is reason why I've gone to the trouble with this machine, the engine is a bit of freak in that it's always been stronger than other BG 86's I've used. In particular, it revs harder and has terrific throttle response.
Here's hoping this fix holds up.
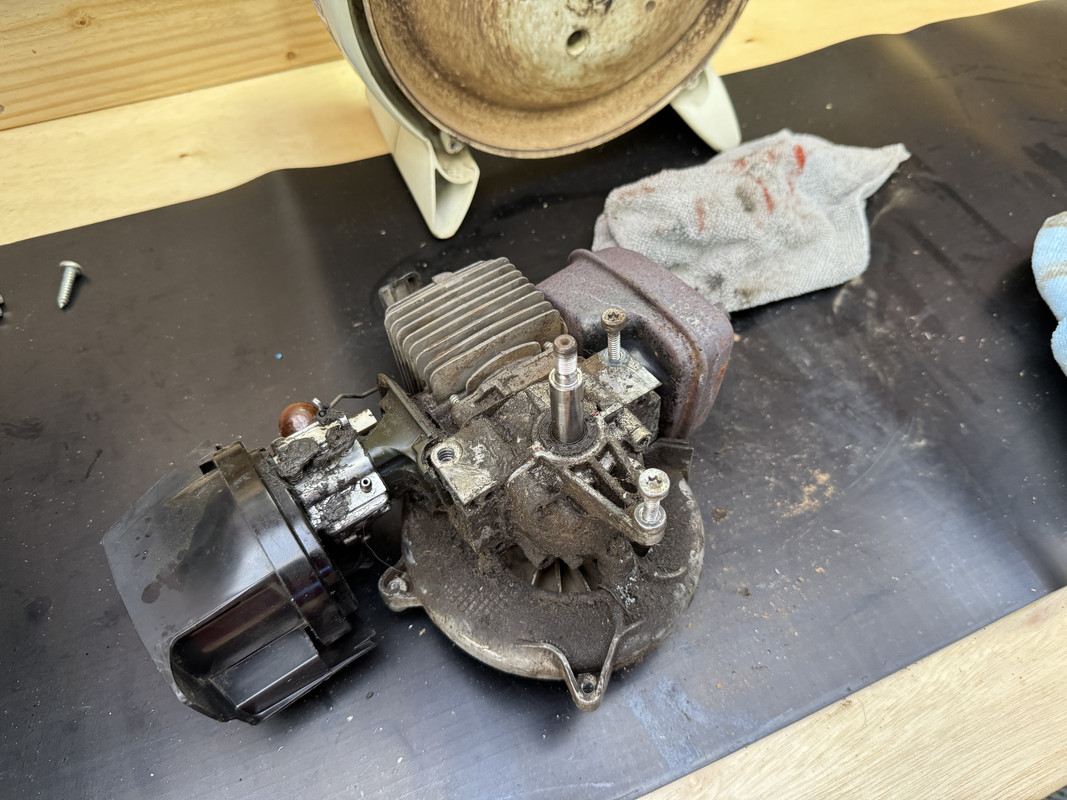
That is a complete engine assembly for a Stihl BG 86 blower sitting out of the plastic chassis. This machine I had to sideline for a brand-new blower because it kept breaking the recoil spring. I assumed it was something to do with the crankshaft bearings as something didn't feel right when pulling on the rope. I didn't have the time to mess about, so it got put away for parts.
A few weeks ago, I pulled it down and found that the engine was loose in the chassis, which was causing it to flex and twist when being pulled over, in turn putting more strain on the starter and starter spring. Hence the breakages. As I stripped it further, I then discovered someone (the dealer) had tried to remedy this with a coarse thread timber screw. Of course I was never told this. So, I thought perhaps I could have a go at doing this repair PROPERLY. Once again, this is why I am doing these jobs myself, no one gives a sh.t and I'm fed up paying for such incompetence.
This shows the damage caused, the timber screw had wallowed out the threads. There are three of these to hold the engine assembly to the blower frame, the hole should be for a M5 fastener, well its beyond M7 here...........
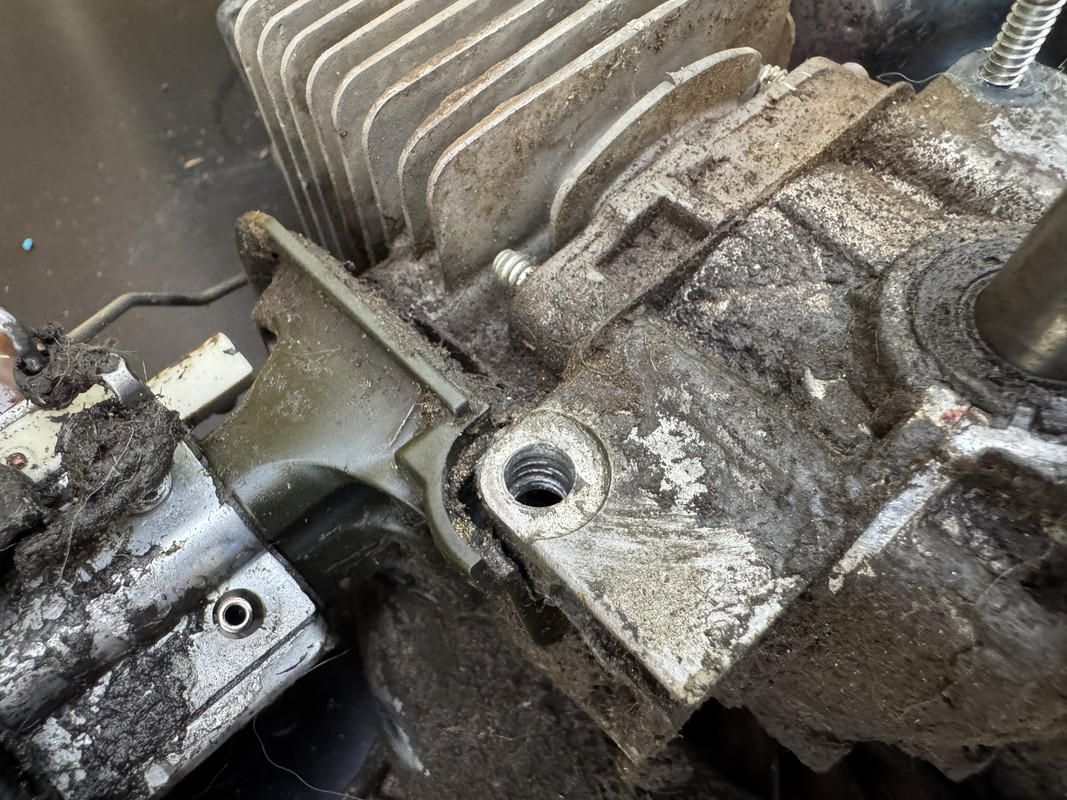
So, after some recommendations, I grabbed this Helicoil kit from Supercheap. Because of the damage, I had to go up to an M6 fastener, which I had on hand after buying an assortment of Stihl hardware last month.
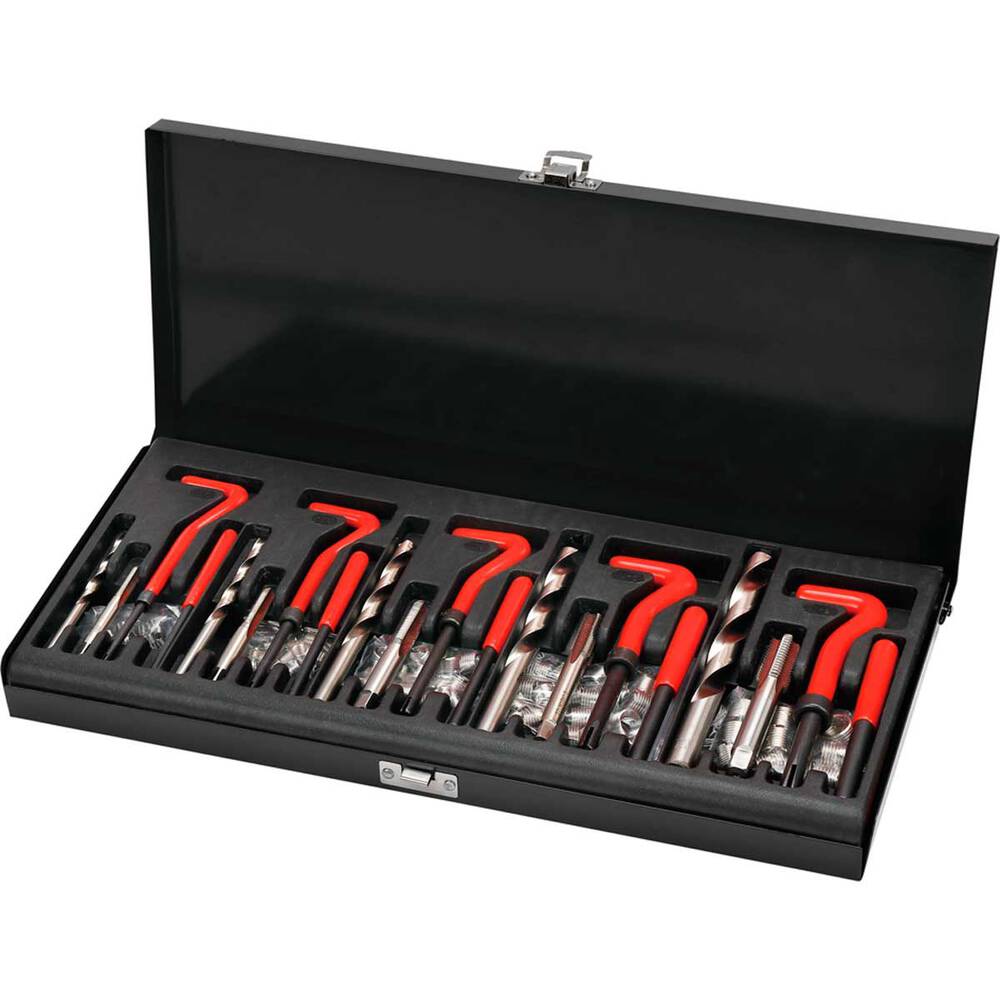
(I paid cash for this kit, much to the bemusement of the young lad on the register, took him a while to figure out how much change to give me.

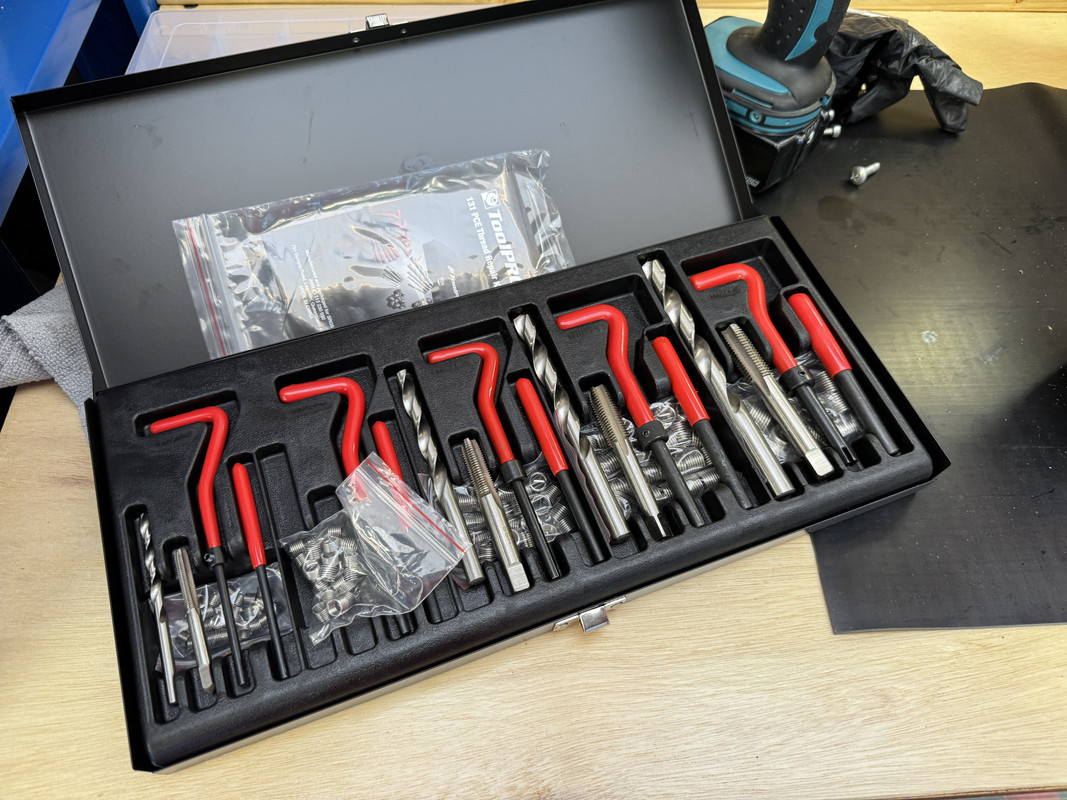
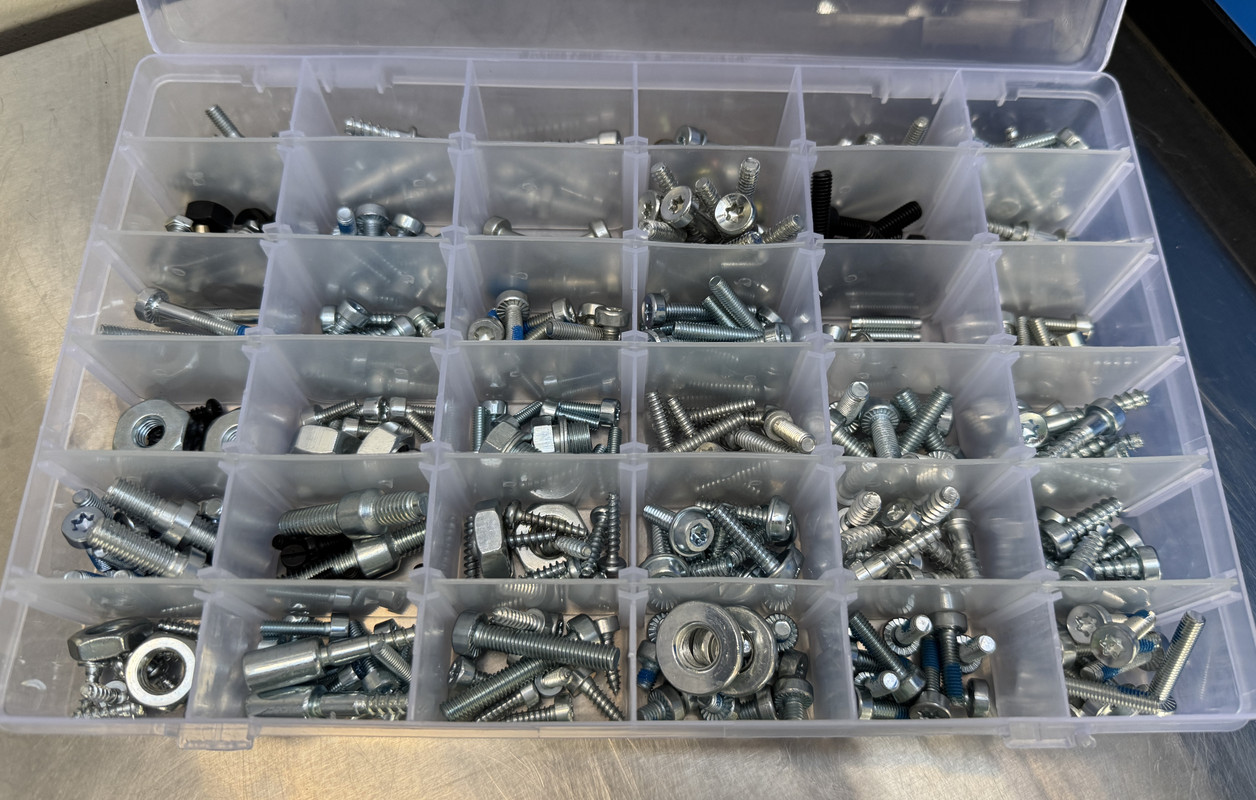
I have never used a Helicoil before, let alone a thread tap. Because of how flogged out the hole was, the supplied drill bit was only used to finish off the work of the wrongly used fastener. The tap threaded in and started cutting smoothly, which was used with some lubricant and the occasional back and forward to help it along. As always, I watched how to do this multiple times, many thanks to the Mr. Dactyl.....................
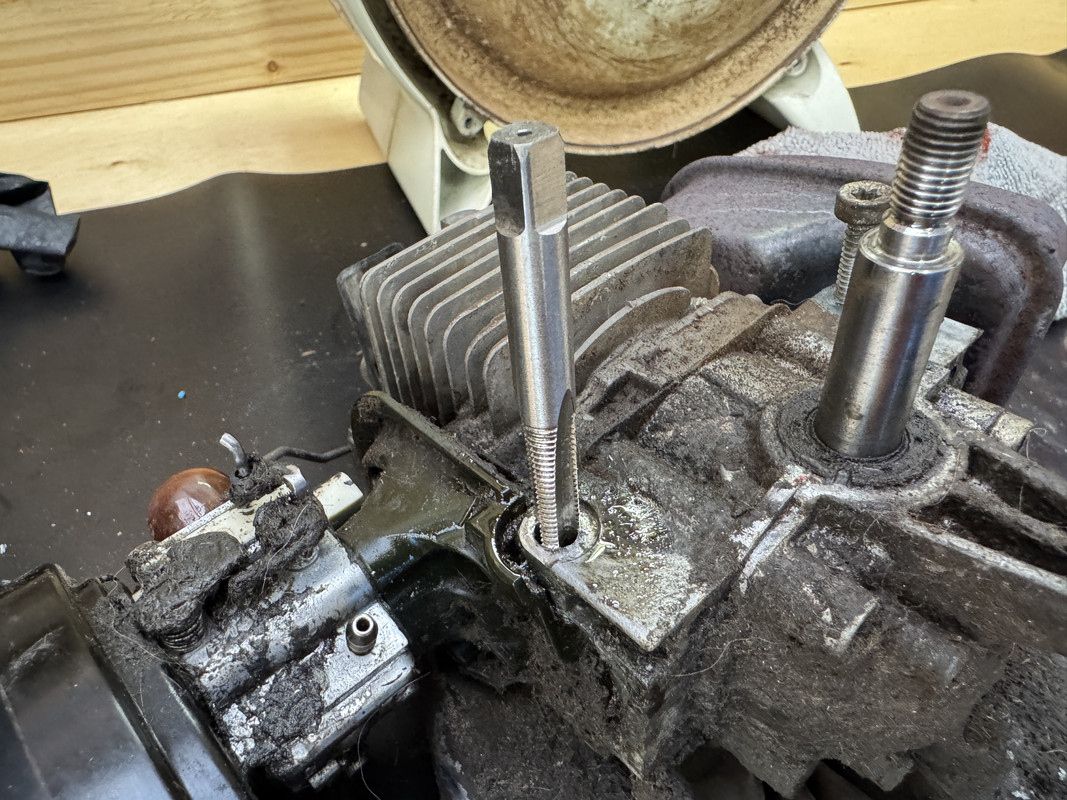
This hole is an external pass through, so no chance of metal chips entering the engine. The Helicoil insert is then wound in with the supplied install tool, the winding tab then broken free with the supplied punch. I had threads again!
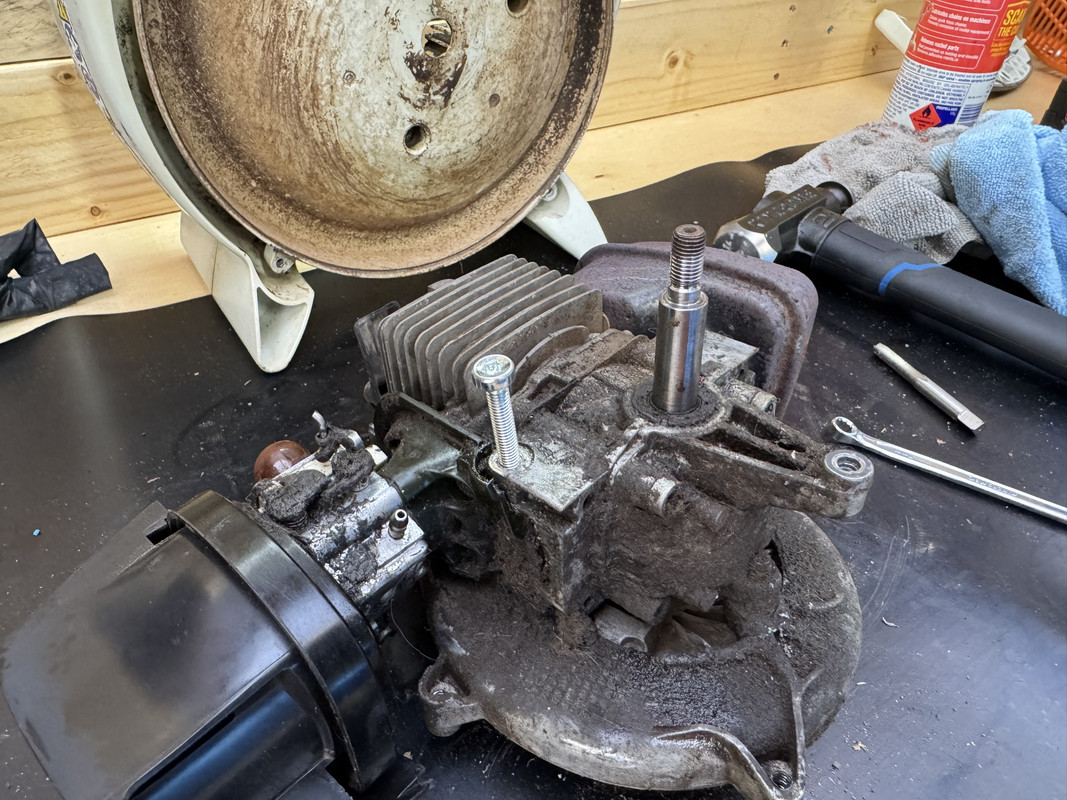
Then it was a case of putting it all back together again. This involves reconnecting the fuel lines before aligning the engine unit back into the frame and the bolts tightened down, the repaired threads torquing nicely. The fan is then put back on the crankshaft with a washer either side, followed by the reverse thread nut, followed by the fan cover. On the other side, the throttle rod is connected to the trigger and the kill wires hooked back onto the coil. From here, the front cover/recoil is reattached, and the blower tube reconnected, which on this machine needs the assistance of three tek screws to hold it in place.............the result of working a hard life.
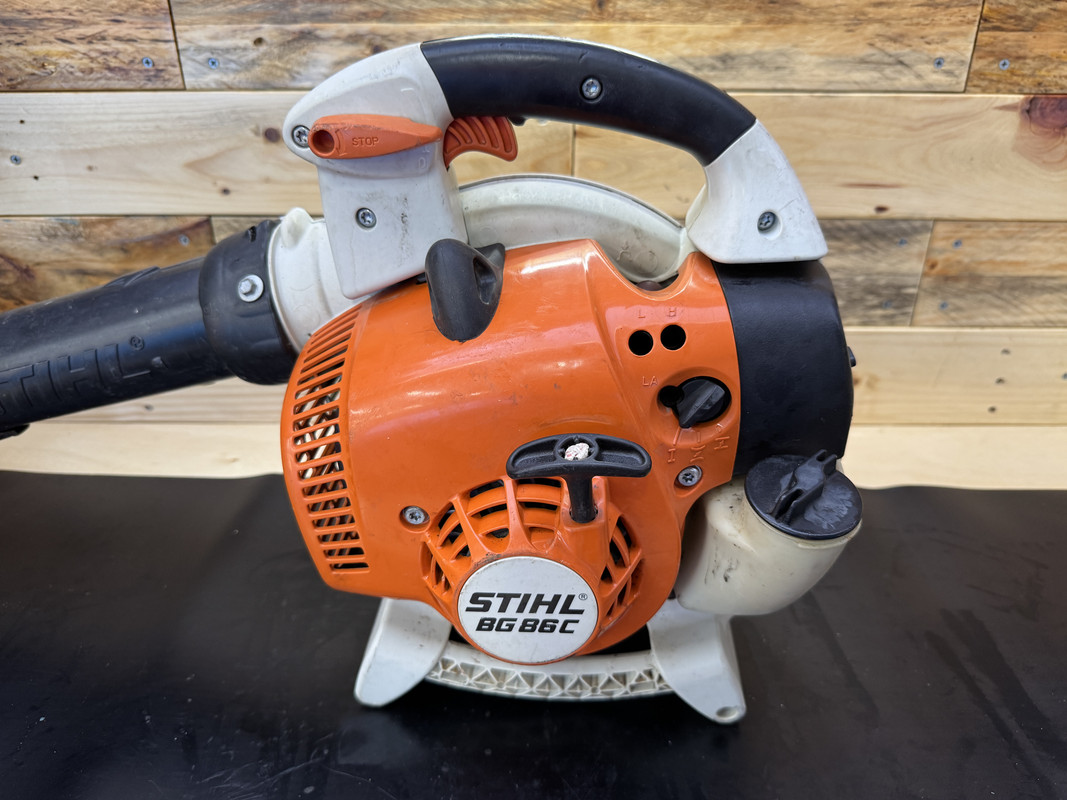
Having used and worked on countless examples of these blowers since 2002, I know them inside out. There is reason why I've gone to the trouble with this machine, the engine is a bit of freak in that it's always been stronger than other BG 86's I've used. In particular, it revs harder and has terrific throttle response.
Here's hoping this fix holds up.